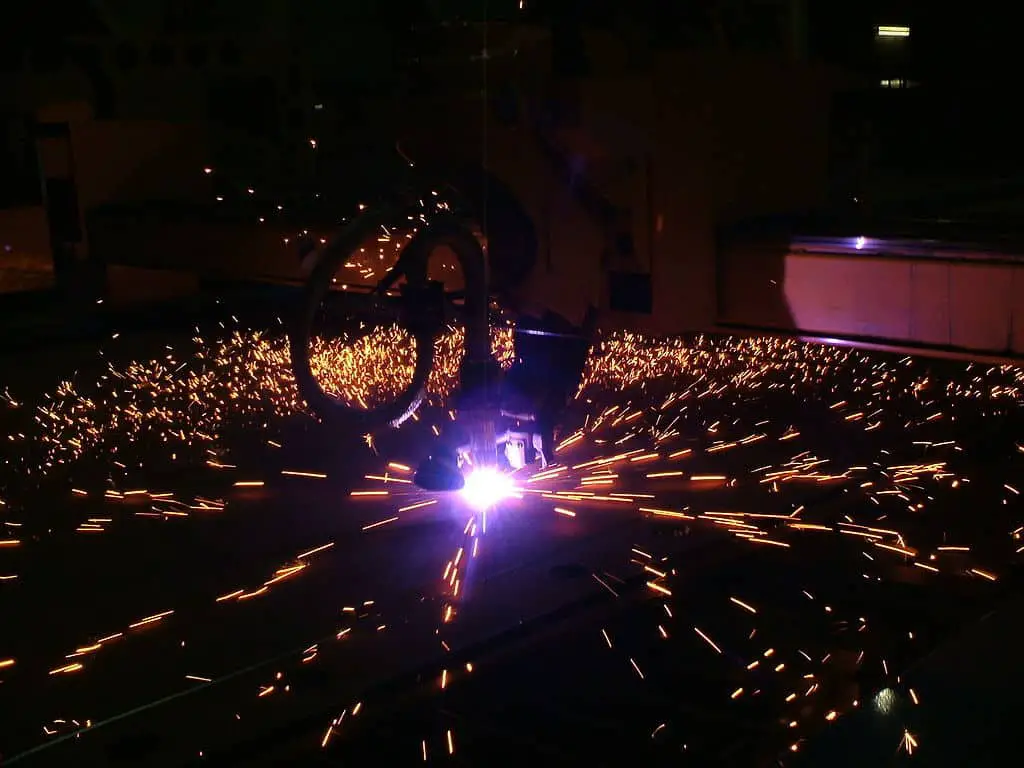
Many of us have wondered at least for one time that how do people precisely cut materials like stainless steel, aluminum, brass, and copper? Well, they basically use a technique called plasma cutting which is done by a plasma cutter.
But it’s true that this type of cutting requires some prior arrangements in order to effectively do the work. Today we’ll learn all about how to use plasma cutter in this guide.
So let’s begin:
What Is Plasma Cutting?
Plasma cutting is a process that involves precisely cutting down materials such as aluminum, & stainless steel into pieces by using a plasma cutter. The main mechanism behind this process works by establishing an electric arc to melt the metal while supplying gas at high speed from an air compressor.
You can effortlessly cut a diversified range of materials by using this process which can’t be possible by using oxy-acetylene cutting techniques. The process is also very fast and less risky compared to other cutting procedures. You can have all the materials and tools at an affordable price. In fact, there are some plasma cutters that are portable meaning you can use them portably in outdoor areas.
Plasma cutting also produces less amount of scarps in compared to other processes. Besides, the quality of the finished metal will be way better and the machines are very easy to operate.
Application Cases
Because of the efficiency of plasma cutting, there are numerous areas in which this process is primarily used for accurately splitting up metals into pieces. In fact, a bigger portion of the area is the repairing industry. Apart from this, plasma cutting is also used in the largest manufacturing industries including vehicle and shipbuilding and also construction and service centers.
Advantages
- Can cut a large number of materials including the major ones
- Can effortlessly cut having a high amount of thickness
- Features faster cutting-speed
- The whole operation is quite cost-effective
- Features quality cutting with fewer scarps
Disadvantages
- Can consume high electrical power
- A bit costly than the oxy-acetylene process
- Can generate a high level of noise
How To Use Plasma Cutter?
Now that we know what is plasma cutting and where it is used, it’s time to learn how we can actually use a plasma cutter step-by-step like the way a professional operator does. So let’s begin:
What Are The Required Gears?
The required tools and gears can be divided into two sections one will comprise of all the personal safety gears and the other will include all the essential plasma cutting tools.
Personal Safety Gears
- Safety Helmet: Plasma cutting produces not high but a considerable amount of sparks and flames while performing the operation. This requires you to fully protect your eyes and face by wearing a safety helmet which is quite similar to that of a welding helmet. You can easily get it from any metal fabrication store.
- Safety Glasses: safety glasses should be only used if you don’t have any safety helmet. In fact, if you just spend hours and hours of your time for months observing the operation open-eyed, no doubt, it may gradually cause serious damage to your eyes. So you should at least put on safety glasses during plasma cutting.
- Fireproof Jacket: this is very important. A fireproof jacket will not only protect your upper body from all sources of fire, sparks, and flames but also your body will be safeguarded against touching any hot metals that may burn your skin.
- Shock-Resistant Gloves: working on plasma cutting can be very risky for your hands if you don’t wear any fire and shock resistant leather gloves. Because our hands and wrists are the only body parts that will stay in close proximity with the metals that are being cut out using plasma. These gloves are a must for this operation.
- Fire-Resistant Chaps: unlike jackets, chaps will protect your lower body area including legs from fire and flames. Wearing this cloth is as essential as wearing a fire-resistant jacket in order to protect your overall body.
- Fire and Shockproof Boots: this is another most important gear on the list. Since plasma cutting operation involves cutting down unwanted pieces to splitting something into several portions, hot metals and scraps can anytime drop over your feet and cause burn to your legs. Hence, it is your due responsibility to wear fire-resistant boots before working with any plasma cutter.
Plasma Cutting Tools
- A Plasma Cutter Machine: this is the first and foremost thing you need to have in order to perform plasma cutting over any material. This machine basically runs by electric power and come in with different cutting features. You just need to buy one that comes with standard cutting power according to the type and thickness of your workpieces.
- Air Compressor: plasma cutting relies upon air compressor in order to perform its operation. But it’s true that many plasma cutters now come with this feature built-in. But in case your machine doesn’t have one, you’re required to buy it separately. Besides, buying a bit large compressors will save you from waiting in between the operation; otherwise, you can do it using any compressor.
- Moisture Filter: as the name suggests, this filter is designed to supply dry air into the plasma leading you a secured cut of your workpieces. This thing is worth spending money on.
- Wire Wheel: this thing is basically a grinder which is used to remove all sorts of paint and unwanted substances from the surface of your workpiece. Besides, it’s a true fact that paint is very flammable. Working over materials that have paint over it can be very dangerous. So you can use this wire wheel to rub those substances off the workpiece.
- Ground Clamp: this is very important. As with working over any electrically conductive materials, we should ground the material in order to avoid our body from getting any electrical shock. You’ll need to attach this with your workpiece before performing any cutting operation.
Conditions Required For Your Workplace
Plasma cutting produces a high amount of toxic fumes and gases which can easily get mixed with your living atmosphere. Besides, inhaling this can cause serious damage to your health. So we should definitely work in a well-ventilated area.
Step By Step Usage Process
- Put On Your Safety Clothes: as safety is our first priority, the first thing you need to do is to wear all the safety clothes and gear before even holding the torch. Now this will include putting on your fire-resistant jacket and chaps. You’ll also need to wear your safety glasses and gloves for protecting your eyes and hands. Not to mention, the final most essential item you need to wear is your safety boots. This will do for now.
- Clean Up Your Workpiece: now take the wire wheel in your hand and clean the workpiece from all sorts of paint, dust and other unwanted substances. Otherwise, you can just use a sponge or any typical brush to clean it off from dust only.
- Ground Clamping: now you need to attach your ground clamp with the workpiece you’re going to cut. As said earlier, this will secure the workplace condition and also take away any excess heat from the metal.
- Connect The Cutter With Air Compressor: in this step, you’re required to connect the air-compressor with your plasma cutter by using a male and female gas hose. Afterward, switch the airflow on.
- Configure The Cutter Machine: now you need to select the appropriate amount of amperage in order to proceed with your operation. The temperature will be based upon the thickness of your workpiece. A rule of thumb is to use 60-80 amps of current for cutting a material having 1/2 inches of thickness.
On the other hand, a cutter having 25 amps of power is enough to cut down metals having 1/4 inch thickness otherwise; you’ll need a cutter that features a high amperage of power in order to effortlessly cut down thicker pieces of metal.
- Power Up Everything and Begin Cutting: now turn on your cutter machine and grab the torch in hand. Most often you’ll notice a trigger lock covering the switch. Now pull it out and hold your gun onto an exact 90-degree angle from your metal and initiate cutting.
A general rule is if the sparks generated from your operation doesn’t flow underneath the metal, chances are the amperage settings or your cutter machine isn’t capable enough to cut this metal having any given thickness. Otherwise, you can just increase the amps.
- Have An Appropriate IPM and Move The Torch Slowly: the IPM stands for inches per minute. This basically means how fast you should or can cut a metal having a certain figure of thickness. The more amperage you set, the higher the IPM will be. If it takes too much time, then guess what, you need to increase the amps. But you got to keep moving the torch slowly towards the end.
- In Case Of Gouging and Piercing: for gouging, you’ll need a gouging tip that you’ll attach into your torch. Now hold your torch at a 45° angle from the metal to perform the task.
In case of piercing, you need to be a bit tricky. At first, you need to hold the torch with the gouging tip and put it at a 45-degree angle from the metal. Now turn on the torch. As soon as you see the sparks are flowing underneath the metal, just change the angle into 95° and make the hole.
- Finally Close Everything Retrospectively: finally, we need to switch off everything & wrap up all the hoses including the ground clamp.
Measures To Ensure Safety
Plasma cutting is a high fire-intensive process that can go wrong anytime if we accidentally make any mistakes. So you are required to place a fire extinguisher in near proximity to your working area so that it ensures the overall safety.
Final Words
Knowing how to use plasma cutter can be easy but mastering it flourishes the actual performance and efficiency of working over large projects. We believe this guide has provided you with all the critical details about effectively using this machine which will be helpful for you in practice.
Thanks for reading the whole post. Stay along with us for our upcoming welding-related articles.
Information contained on this page is provided by an independent third-party content provider. Frankly and this Site make no warranties or representations in connection therewith. If you are affiliated with this page and would like it removed please contact pressreleases@franklymedia.com